Well, it rained this morning, so it is time to start my summer project and thought I would share the process I use and the steps I take along with some of the tools used.
First: When it comes to hand polishing and blending, the biggest mistake newbies make is the
first question they ask (what steps in order do I use) Hand polishing is an art that takes practice to get the feel you need to go through the process of blending. I call this "the art of the scratch". That is what polishing comes down to knowing the different scratches and how deep they are.
When polishing out scratches, you have to use a finer grit to get out a courser grit scratch. This is done by never going over the same direction. What I am trying to say is if you sand in one direction then go over that in another direction (keep changing directions). This slowly bring the material around the scratch down to the depth of the scratch until it is gone.
SO, to answer the question on steps it is up to you to get the feel for removing scratches (it's not steps it's a process)
One rule I lived by over the years for hand polishing is, all ways start with a finer grit because you can all ways go to a courser grit but if you start out with a course grit and didn't need to you have just crated more scratches to remove. Follow this rule and you will soon find yourself learning how deep scratches are and where you need to start in polishing the out. (The Art of the scratch)
Here is my summer project:

This one has been kicking around for years, fist built for my wife as a way to keep building
Mostly use for trying out different polishing and painting techniques.

This is the same pistol I worked on in the trigger post. I like to build up a pistol getting all the inter parts all working, then run some rounds through them with stock parts so I know it is a shooting pistol from the start.
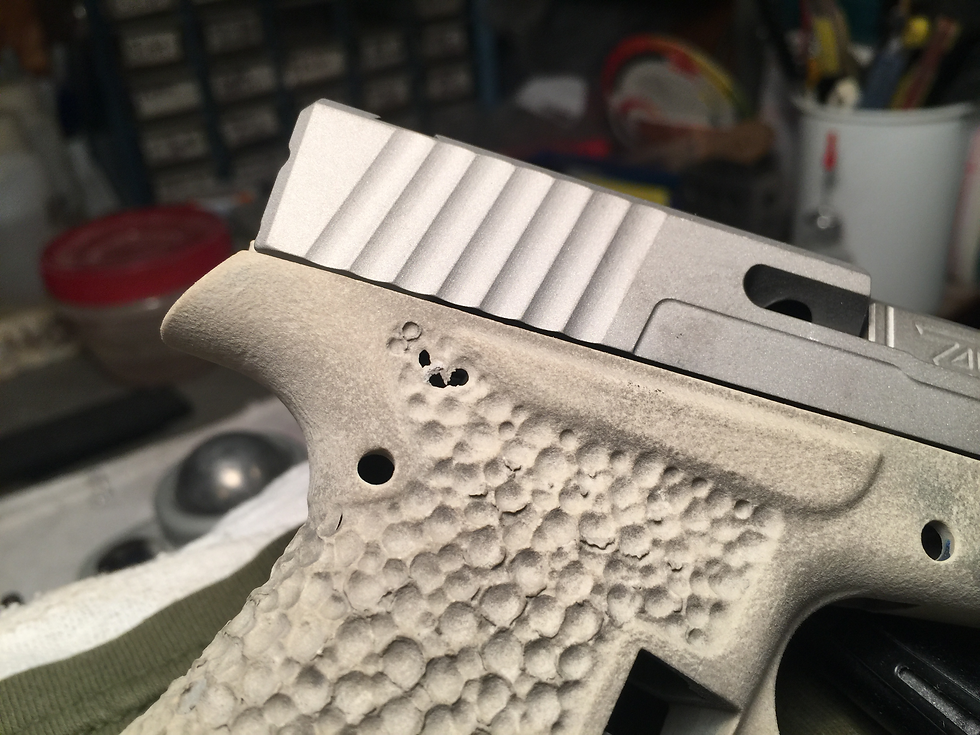
As you can see I have some repair work to do. This is my second attempt at stippling, I should have practiced more but no big deal this can be fixed. I'll go through the step I use to fix this but first I need to clean up the sand blasting first. You can see how blasting didn't get all the paint off. Just a guess on my part but this pistol had at least four coats of paint. I didn't want to over blast it because using a course blasting sand would just make more polishing work in the long run, so I'll sand the rest off.
When I start a build, I try to have a plan or theme at the start. I've been thinking about a Black Widow build for about a year now, this could be the one that gets the Black Widow theme.
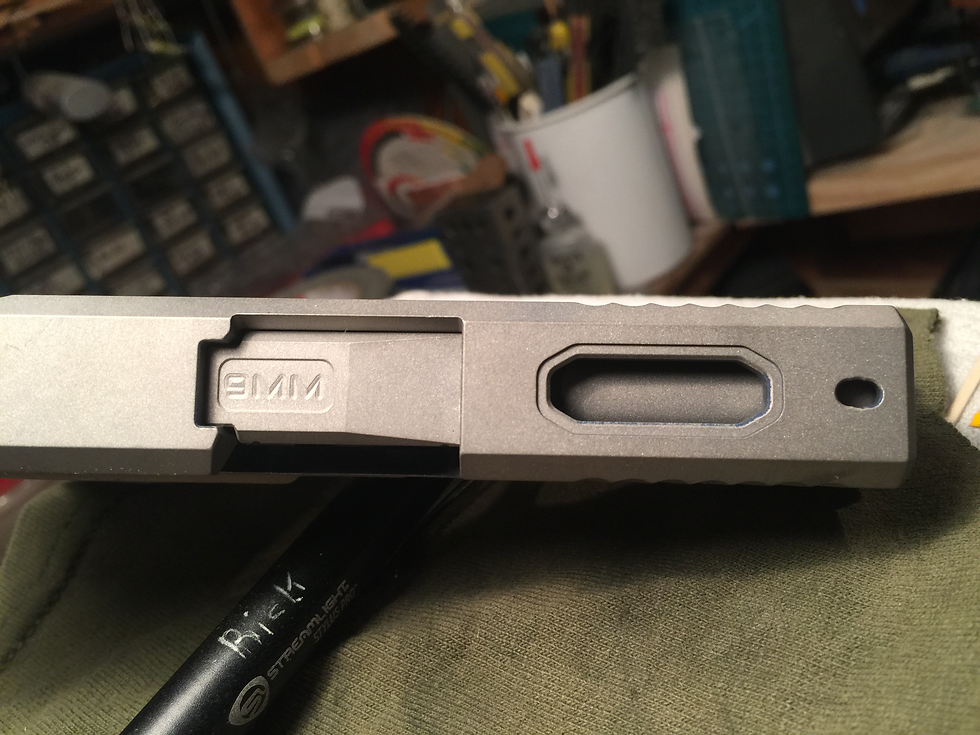
Here's my plan:
The pistol is going to be a flat black with a spider web draping down from the center of the slide cut.
In the center of the slide cut on the barrel I want to put a spider etched in the barrel. The look I am going for is a spider in the center of the web. I'm not sure on the web color yet. Not sure if the web should be the same color as the grip or not. The stippling has to be painted because for the hole fixing with JB Weld.
JB Weld doesn't stipple (believe me I tried)
I would like to use a clear pearl coat for the finish but I will need to test the pearl, I never tried pearl clear coat yet.
Will see how it all folds out.
BUT first I have some sanding to do.
I'll post more as I go and hope this helps those that want to build that one-of-a-kind build some helpful info.
by Hawkeye » Sun Jun 19, 2022 12:11 pm
I was up last night watching the planets and thought about how to I can use a straight edge to lay out straight lines. I think I will give that a try next. With the pattern I am looking for I think it has to be straight without being crowded. I'll figure it out if I think about it long enough.
by Hawkeye » Sun Jun 19, 2022 12:06 pm
I have tried do a HD border but haven't got it close to Will's. I think he must lay out his borders before he paints. His HD borders look like they are polished and the only way to do that would be before paint. It looks like he might have used a 3m pad, maybe one on a wheel. He might use sandpaper to get the outer edge flat without a plastic build-up like the inside border. I am going to try a HD border in one of my next builds.
by WE4PONXYZ » Sat Jun 18, 2022 11:18 pm
I keep coming back to see the progress and bro I’m loving it. I take mental notes every time, keep up the great work. You are a much talented man and it shows through your builds. If you wanted to achieve something more akin to a web on the stipple. I would suggest a hyperdrive (check Gledhill) or circular pattern on the grip side panels. Use the same tip, and overlap slightly and it should give you almost a twist on the outer edge of the circles.
ou could start your circle at either the center or start at a corner for a different effect. I practice on a similar polymer box as you do and it’s pretty damn close to the same melting point as the frames. Closest and cheapest thing I’ve found yet and lots of real estate to practice on. Been working on perfecting my HD borders, and I know you recognize that pattern Hawkeye…
I can’t wait to see it all finished with that one-of-a-kind Hawkeye look!!!
by Hawkeye » Sat Jun 18, 2022 3:51 pm
Ancient Order wrote: ↑Fri Jun 17, 2022 4:09 pmPersonally, I like the stippling the way it is. Reminiscent of a black widows web, which is always a little "messy". Thanks for posting. This is awesome! Thats kind-a of what I was looking for in the sides of the grip. I wanted a woven look simaler to a web but a lot cleaner look, for now I'll leave it. I know I can do better. I am doing this right-up to show guys it is not hard to take your build to the next level. It takes patience with a plan mostly. As far as paint, some of my first builds I used can paint. You have some nice builds ready for the next step, I am here to help.
by Ancient Order » Fri Jun 17, 2022 4:09 pm
Personally, I like the stippling the way it is. Reminiscent of a black widows web, which is always a little "messy". Thanks for posting. This is awesome!
by Hawkeye » Thu Jun 16, 2022 2:27 pm
I am not a painter!! but I try. I can only relate what I have experience with (trail and error) OK let's talk about what little I know about painting: First you need a place to paint and to cure you paint. Here is where I do my painting. I keep it set up all the time because I am building and painting stuff often. I even paint some of my jeep parts and fishing jigs.
Home made paint both with a shop vac for ventilation with a small fan next to it.
I keep the shop door open just in case of paint fumes building up plus I use a painters mask (a must have) more detail later.
This is the cheapest way I could find for a paint cure oven. I think I have $115 plus free shipping. I'm sure it costs more now.
I got this tip from watching u-tube stuff on painting. A hemostat set is the easy to use for holding parts and can go from the paint both to the cure oven without having to touch your parts being painted.
Here is some other things that will help keep the painting process easy.
1) A painters ventilation mask. A MUST HAVE!! you don't want to breath the fumes, you will die!
2) Digital scale- with cerakote paint you have to mix two parts and you need to know the ratio for mixing. I use KG GunKote you don't have to mix but I do use an additive. more on this later.
3) Acetone is the best clean-up stuff and you need to use it to keep your airbrush from clogging up and for cleaning jars.
4) I keep some acetone in smaller jars for easier clean up along with a paint jar with acetone for running through the airbrush after painting. More later.
5) 180 additive and paint, well talk more detail later.
6) Q-tips for cleaning along with some pipe cleaners.
7) I use dowel sticks for mixing but you what ever you have.
Let us talk about airbrushes:
1) This is the one I have use for years now. Bagger single-stage airbrush. Single-stage means you press down, air comes out, pull back and paint comes out. The more you pull back the more paint comes out.
This for beginners, simple to use. This one has three different size nozzles for a wide spray or smaller narrower sprays but not for a fine line spray. This is a syphon type brush which feeds from the bottom with a jar. Jars hold up to 3/4 oz of paint. This works best for me, 3/4 oz is enough to paint slide and frame for a PF940v1/C and 1/2 oz is fine for a PF940sc or PF9ss
2) It is hard to see but this one is a two-stage airbrush. Two-stage means that if you are not a beginner don't use this one I used it once then after cleaning I can't get it to work any more. I know I know it is something I did and I haven't had time to figure it out yet but I will. I have some plans in the future for some real nice airbrush work as soon as I learn it. Two-stage works the same but also has a manual setting for how much paint comes out. They all so come with tree different size nozzles for wide to thin spry patterns. Two-stage airbrushes are what you need for fine detail painting. Most come with a gravity feed paint cup on top of brush that hold small amounts of paint.
You have to have a pressure regulator for any kind of air spraying. I run mine 9-14 psi with a 190 psi main line feed, this is because I run a big air compressor but you don't have to have one for airbrush painting. I use to use one of those cheap 3 gal. tank air compressors until it died. The main thing to remember is you have to have a steady air pressure for the airbrush to spray a constant even flow. How you do that is up to you.
I use KG GunKote because, ONE that is what I started with, TWO I don't have to do the two part mixing
THREE has a long shelf life. As you can see, I have a wide selection of paint, so I want it to last a long time. I can not talk about CeraKote but it looks like that is the gun painters choice.
Will I ever go to CeraKote? Maybe when I use up all my KG GunKote. I am happy with how it turns out. It has a Hard finish and doesn't scratch. I like using there 180 additive.
180 Additive- you add drops based on how much paint you use, 1 oz paint=16 drops, 1/2 oz paint=8 drops, and 1/4 oz paint=4 drops. After painting this lets you lower the cure to 180 degrees. I set my oven to 200-220 degrees. There are two reasons why I like using this, one is I don't have to worry about getting my frames to hot causing nose droop or warping of the frame. The second is when masking off I can leave 3m heat resistant tape or stencils on during cure time. When you mask off detail stencil stuff you can leave them on for curing, sometimes if you try to take them off before curing, you take the chance of pulling paint off.
I am constantly learning new painting stuff or mostly learning why and how I messed something up.
Now to what I have learned painting this build.
If you shake up clear coat to much you will put air bubbles in it that will make your paint turn out milky or have small bubbles, it the finish that looks like dust trapped in the paint.
Paint like gun metal gray and black chrome or pearls need to be shaken up to airbrushing because it will settle out faster than just a paint color. I think this is because of the additive that gives it the color doesn't mix well with the paint.
Cure time matters, when painting with a flat color takes less time than a satin color.
Flat paint= 1-1.5 hours
Satin or high gloss paint= 2.5-3 hours
Over curing is bad too, cure to long and paint may peel, not long enough paint scratches easy and has not set. (Still soft)
I was disapointed in the black chrome paint I used. I like it but it wasn't what I had in mind for a black chrome look. The KG GunKote black chrome is more like a dark gun metal with silver flakes. Still looks good with the high mirror polish but not what I had in mind.
I all so learned that clear coating a mirror finish will change the mirror look to a glossy shine that takes away from the mirror look.
I should have mentioned that I mask off the grip area. I do this because you have to make sure you get all the paint off your grip. Paint does not stipple (I know the hard way) (JB Weld does not stipple ether) Remember that heat resistant tape and stencils can be on during cure time. TIP: when using heat resistant 3m tape and stencils, they can be heated with an hot air gun to make then stick better and to soften them so they can be pressed into corners. I do this just before painting to get a good stick so paint bleeding under stencils will not happen. When I cure a frame with grip masked off I will leave them on until it is stippling time. If you use the rubber stick on grips you can do an oven bake on at 150 degrees for an hour and that stuff will stick for ever.
I had a chance to do stippling yesterday so here is what I decided to go with and how to stuff.
You have to have one of these, really you need one or its slow death so use one.
1) This is really over kill on the stippling tips. I save stuff and over the years I have accumulated a bunch of tips from wood burning kits and soldering kits.
2) This is the one I like to use (OT defense iron 30w) I like the short head, it makes it easy to use with less stress on your hands. I have tried three other irons, they are longer and are 25-80 watts. What I found is its not the power its the feel you have with the iron you use. If you use an iron with lots of power you melt faster and loose some control over your burn. A low power iron you have control but takes longer to melt. Its not much difference just in seconds but its the feel and pressure you use to burn a pattern in stippling. Its like this, you burn and it is what you are looking for, now repeat it,
then repeat-repeat-repeat and so on. You have to get the feel and repeat it over and over.
3) You have to have a way to clean your tip, here I use a wire brush and a soldering iron cleaner. It is just brass shavings that will clean plastic off your tip just by swirling your tip in the curled up brass shavings. You really need to clean the tip often. If the tip builds up plastic you will loose the detail in the tip and your pattern will not match so clean often.
It really helps to have something to practice on. Here you see how I tried different tips so I would have an idea on how much room they would take up and how the pattern looks. What I decided was to use a small circle pattern instead of a larger circle pattern because of the area I had to stipple. This is a PF9ss, its a small grip so the room for a large pattern is not there.
Now let's see where I'm at now in this build,
went with two deferent patterns because I had to have a small random pattern for the back strap on the grip. The detail around the logo is to small of any thing large. I should have left a border on the frame to work to and from. This is poor planning on my part but sometimes things just keep changing when building, its hard to see that far ahead then plans change from step to step.
I like this pattern, it give the woven look. It would look a lot better if the stippling job was better. Actually the stippling on this grip sucks. Lines are not straight in the pattern. The circle tip burn should have been spaced out better its just not a Shogun Customs. I may redo this.
You may ask, How can you redo a stippling job? Thanks to a tip from Mooner you can use a large flat tip to melt the grip back to a flat surface and then you can reburn a pattern. It does work, I have use this tip on some earlier attempts at stippling.
I will leave it as is but I really think I will redo it but for now I need to do a final polish on the slide. I need to clear coat it with something for protection from surface rust. The high polished stainless steel slide is ok but the sandblast web needs to be covered so the whole slide will need a coating. I'm still working this out.
by Hawkeye » Wed Jun 15, 2022 8:02 pm
Ancient Order wrote: ↑Wed Jun 15, 2022 6:20 pmLookin good! I'm a definite sucker for information, so would appreciate how you did the painting. Are you going to paint the spider black? I got to hot working outside today, so I plan on doing indoor stuff tomorrow. I'll do the paint process right up then. I hope to do the stippling too.
by Ancient Order » Wed Jun 15, 2022 6:20 pm
Lookin good! I'm a definite sucker for information, so would appreciate how you did the painting. Are you going to paint the spider black?
by WE4PONXYZ » Sat Jun 11, 2022 8:40 pm
Staying tuned like a 90’s after school cartoon. Can’t wait to see it finished in all of its glory.
by Hawkeye » Wed Jun 08, 2022 7:22 pm
MAN!!! Check this out:
Its really hard to get pictures of a high polish like this sorry
I should have all the painting finished tonight, I an getting so excited this is on the down hill now.
I may finish up next week some time depending on how the fish are biting tomorrow night.
Just before a full moon in June is the best time to night fish, Going to Dale Hollow Lake in upper TN.
I have pictures and can do more right-ups on the painting process if there is any interest in it. It seems like the detail stuff of this build is losing interest to folks.
So here we are at the last step before assembling:
I wanted to put Black Widow in the spot that you see Hawkeye but I couldn't get the stencil to weed the detail right and ran out of stencils to use for it so, Hawkeye it is. To be hornist, I have been thinking I should put my name on all my new builds, after all there all one-of-a-kind builds (I did that) stuff LOL
Now I need to make a stippling tip. I want to come up with my own style and a pattern but this is something I all ways seem to struggle with. At this point in a build I start second guessing everything.
My stippling skills are average at best. Well By the end of next week I should have this build finished and in the safe.
by Hawkeye » Fri Jun 03, 2022 8:11 pm
WE4PONXYZ wrote: ↑Tue May 31, 2022 11:34 pm Yeah, I got to the point your at now at went “uh no.” Soo I went to work with the half round to reprofile and get rid of the pitting and then switched to the wet sand high grains and buffing wheel to give it a mirror polish. NEW PICTURE The slide lock release cleaned up nice. Looks like it had to just take off more stock then I thought. it still shows some pits but not as bad. I think I can use it now.
I'm still up in the air about painting them silver, It all depends on how the paint turns out on the frame.
I did get my Glock magazines in yesterday so, I will be switching out that clear plastic crap that may or may not work depending on the day.
I made some test pieces for paint testing by polishing up some scrape steel then sandblasting a strip like is on my slide. This way I will have an idea for how the paint theme will look on a high polished slide. Another concern I have is what will happen to the sandblast web.
A) is a satin clear coat, you can see that the sandblast is still seen but the high polish is gone.
B) is a peal clear coat, you can barely see the sandblast web.
C) is base coat of silver, then black chrome and then a thin coat of clear pearl. You really can't see the sandblast any more, but I really like this combo, I think I will use it on the Dragon build I did last winter, It has some bad paint runs on the slide that drives my nuts every time I take it out. But not what I want on this build.
D) is a flat black base coat, then black chrome with clear pearl. This is the way it was suggested in a video by KG GunKote for using black chrome. this is nothing like what I had in my mind of how black chrome would look. Sandblast is completely gone.
So where are we at now?
I am not a painter and I have very little experience with colors and using airbrushes but I do try.
From testing so far, it looks like painting the slide even with a clear coat (that's not clear ) is something I need to rethink. The reason I wanted to put a clear coat on the slide was to cut down on fingerprints and give a harder finish to protect from scratches. I knew that the black frame would not match but I thought I could at least get it to shine. I still have room to do some more test paint, so what I might try is black chrome with and without a clear coat. one with clear satin and one with clear Peral. This will help me zero in on paint for the frame. As for as the slide, I am thinking I will just leave it as is (high Polished) that way the sandblasted web will pop and the mirror finish will still show off all the hand work that has been done on this build, after all I didn't spend four days polishing this to a mirror finish just to cover it up.
Anyone has experience with paint colors please give me some help.
First, I need to relate a lesson learned:
I could not understand why a clear coat would look frosty; well, the reason is I shook-up the bottle too much, putting air bubbles in it. What I think now is a clear coat is just the same as paint but does not have the color pigment added. The reason to you have to shake is to mix the color pigment with the clear coat giving you your color. I did another test without shaking and the clear satin cam out clear satin (who would of thought it ) I still don't think I will clear coat the slide. It gives a polished finish a shine instead or a mirror look.
by WE4PONXYZ » Tue May 31, 2022 11:34 pm
Hawkeye wrote: ↑Tue May 31, 2022 7:14 pm That cleaned up nice!! I was afraid to take it down too much, I think I have a spare in my bow of stuff that I can do some test on. I'll give it a try tomorrow.
Yeah, I got to the point your at now at went “uh no.” Soo I went to work with the half round to reprofile and get rid of the pitting and then switched to the wet sand high grains and buffing wheel to give it a mirror polish.
by Hawkeye » Tue May 31, 2022 7:14 pm WE4PONXYZ wrote: ↑Tue May 31, 2022 6:06 pmWhen I did my two tone silver/black Tyrant slide release I had to take it down another layer or two. I used a small half round file, then switched to 800, 1k then 2 k grit wet before finishing up with a dremel then leather strop. You’ll notice that mine doesn’t have the sharp edges on top anymore though. Still functions the same, just a little gentler on the thumb now. That cleaned up nice!! I was afraid to take it down too much, I think I have a spare in my bow of stuff that I can do some test on. I'll give it a try tomorrow.
by WE4PONXYZ » Tue May 31, 2022 6:06 pm
When I did my two tone silver/black Tyrant slide release I had to take it down another layer or two. I used a small half round file, then switched to 800, 1k then 2 k grit wet before finishing up with a dremel then leather strop. You’ll notice that mine doesn’t have the sharp edges on top anymore though. Still functions the same, just a little gentler on the thumb now.
by Hawkeye » Tue May 31, 2022 4:08 pm
OK! I did the sandblasting today:
Sandblasting work out with any blow out from loose stencils.
You can see their is a definite contrast in the high polish and the sandblasted web.
It's all about the paint now and I haven't a clue on the next step.
I wanted a black chrome but I think it will cover up the high polish I did.
I need a good drink or two tonight and think about the paint job an what to do next.
I am so close to finishing I don't want to mess up now.
Here is another thing I ran into that really bugs me:
I polished up all the bling to match the slide, everything went well until I tried to polish the slide lock release. It is not solid aluminum, it is aluminum cast. The differences between cast aluminum and solid milled aluminum is cast is melted and poured in a mold. After cooled it can be milled, but it has a lot of impurities and get air bubbles trapped so you can't get that high mirror finish like I did on the rest of the slide and bling parts.
My plan is to keep the barrel and bling a high polish with a translucent black on the slide, but with the miss match on the slide lock release, I am not sure? I may have to paint them a sliver.
Still thinking about what to do so any input would be helpful.
by RAMjetta » Sat May 28, 2022 11:47 pm
That gives me an idea for a build I'm working on. Thx Hawkeye
JettaMan OUT!
by WE4PONXYZ » Sat May 28, 2022 6:07 pm
Looking good, I’m super pumped to see this all finished brother.
I want to do something with the grip besides stippling, so this is what I came up with.
This is the logo, emblem or whatever its call for Black Widow. I plan on making this red, form what I see on pictures on the net, the red should pop with a flat black stippling.
This is what I do to make boarders and emblems on the grip area because I don't want to cut into the grip any more then I have to. The grip is very thin and has some really thin spots on the back strap. I prefer to build up with JB Weld and shape as I design.
I use thin silicone baking sheets to make a mold for the design I plan to use. JB Weld does not stick to these silicone baking sheets and they are thin enough to use as a guide for sanding. On this build I was able to use tape to hold it in place but some times tape will cause the silicone to have spaces under it so JB Weld will run under it. When that happens I will use some quick setting glue to hold in down. The glue can be easily removed from the grip before stippling.
I like to mix just a little more hardener in my mix because this keeps the JB Weld form running and it also sets faster.
n this case I used more JB Weld than I normally would use because I wanted to make sure I had enough JB Weld to sand.
First, I use a 600 grit sanding wheel to rough out the shape I'm looking for.
Then I go to my micro sander with a 400-grit sandpaper after removing the silicone mold.
Once I get close but still leaving stock to slowly work down to the height I am looking for, it is time to start working on the detail part of the emblem.
like to use transfer paper, it lets you see where you need to line up you stencils.
I like using this cone shape burs in shaping, I have them in three different sizes, There diamond burs with a 3/32 shaft, just use an adapter to use them in a 1/8th collar.
All Ways leave stock to work off later. Remember you and all ways take stock off but you can not add stock easy. You have to back track. I just hate having to do something over again.
SO, where are we at in the build?
I have the slide and barrel polished up.
I have the frame slicked up and very smooth but I will go over it again before stencils.
I have my Tyrant raw aluminum bling all polished up.
Just a little rant on Tyrant all aluminum bling, all the stuff like mag release, mag base plate, slide rear plate are all solid milled aluminum BUT, there slide stop is an aluminum cast. Not a big deal when you paint but if you want to high polish them as I do in this build, they will not polish up the same. Cast is melted aluminum poured into a mold. This leaves air bubbles and impurities in the aluminum that cannot be polished out so the slide stop in this build will not match the rest of the polished bling parts.
The etched spider turned out great but I got off by 1/32 from being center. If you ask?? Its the spider moving in the web (nailed it)
You can really see all the mods done to the trigger.
I still need to sharpen up some of the edges and sand it down just a bit more but you can see the emblem has turned out good.
Next step will be getting the spider web stencil draped over the build getting it ready for another sand blasting. Give me a few days and I should have a wright up on stencils ready for you.
Before we get into adding stencils lets go over some tools that make it all easier.
1) I like using this 3M yellow heat resistant tape, it has a good sticky glue that when heated with an hot air gun will stick for a very long time even when heated in a cure oven after painting. You need a good masking tape like this because when painting you really need to cure paint before taking off the tape. If you don't cure first you take the risk of pulling the paint off and you have to start over.
2) Razor blade knifes are a must have (X-Acto knife). I use the #11 blade most of the time and make sure you have more than enough blades, and make sure you keep changing out to a sharp blade. Nothing makes me madder than a dull blade pulling and tearing up a stencil you have been working on for half an hour.
3) You will need a good pair of tweezers with a fine point. Believe me you will need a very good set of these. I had to buy a set because my wife would not share her tweezers.
4) A vinyl squeegee works great for getting air bubbles out and for pushing the stencil into tight edges. Another must have tool in my opinion.
5) A cutting board! I have two one is a 6"x8" and one 10"x12", I use them a lot. One way I use them is during masking off. I will lay out tape on the board so I can cut tape into small easy to handle pieces. It makes masking easier, and you don't use as much tape. Remember when you get your stencils on and masked off use a hot air gun to get the glue side to stick better.
You really can't see it, but this is the web stencil.
I have transfer paper on the stencil but one problem I have is locating the stencil on the slide into the right place without being able to see where the web lays out so I had to come up with a way to do it.
Everything centers around the spider in the center of the web, the center of the web is the top slide cut so by placing the slide upside down and cutting out the slide cut it gives me a locator for placing the stencil.
By having a way to locate without seeing the web cuts has worked out great for lining up the web as a center vocal point.
What you see here is the best way I found to control the placement of stencils when doing a full stencil build on a pistol. It gives you a hands free approach so you can weed without trying to hold the pistol too. I don't have a blank mag well vise mount of a single stack so I use an single stack magazine in a vise to hold the pistol to free up my hands. Once I get the stencil draped over the pistol where I want it, I press down all over to get a good stick so when I start weeding I'm not pulling off the stencil.
Here is a great tip you will need if you get into using stencils, all ways pull off in a 180 degrees back. If you pull in a 90 degree you will pull parts of the stencil you don't want to pull. It just gives you more control when your weeding.
In this case because of the detail in the web I removed the transfer paper so I can use my tweezers to weed the detailed web without removing the rest of the stencil. In smaller stencils you can weed before you apply or use the transfer paper to weed parts of the stencil after you apply. Transfer paper is a way to control your stencil for placement.
So, this is where I am at now.
Next week some time I will sand blast the web. To be honest I am worried about sand blasting. I have spent hour of time polishing and all it takes is for one part of the stencils to start coming off during sand blasting that will set me back at least a month. If you noticed I brought the web down into the frame just enough to brake up the line between the slide and frame. I am not sure if doing this will match with the slide texture after blasting but we will see how it goes.
by Hawkeye » Tue May 24, 2022 11:38 am
Next is some custom work on the grip. This will take me most of the week, but I will have some how-to stuff.
by WE4PONXYZ » Tue May 24, 2022 10:58 am
Coming along nicely
by Ancient Order » Mon May 23, 2022 10:38 pm
Outstanding!
by Hawkeye » Mon May 23, 2022 5:43 pm
Finished up my etching today, so let go through what and why I did step by step. first let's talk about tools: This is what I use for my power source, an old manual type of battery charger.
You can use any type of power source but remember it is the amps that determines the amount of time you spend etching. You can use a 9v battery but it has low amps output so it take you longer to etch.
By using a battery charger you can get a higher amp output- shorter the time it takes to etch.
Using the 3amp setting, it does work but slowly but safe because you have more control over the etching process but I assure you will be asking for a faster way.
By using 10amps at 12volts I can etch serial numbers in five minutes giving me .005 deep.
You will need Q-tips (the ones made with cardboard not plastic shafts) cut short.
Something small to hold your solution.
I like to use smaller more flexible wires with agitator clips (easier movement)
and some way to not only conduct current but help hold every thing together.
This trick works for any P-80 you need to install serial numbers on. I took a small piece of metal added a nut and bolt, holding it all with a small c-clamp.
I put the end of the bolt into the bare metal on the frame.
This gives me clean and solid connection for my positive lead.
This how it like to setup my frame for etching serial numbers.
It doesn't matter how you hold your frame but you want to be hands free without any wobble. You need to keep things flat so you can do even passes and you don't have your solution spilling all over.
The reason you need to use cardboard shafts is they will soak up you solution and help with a solid connection, also make sure your clip is on the cotton, this will help too.
Don't forget to have a good respirator, this is a must have.
You want to make sure you soak your Q-tip and keep dipping it to stay wet.
keep moving slowly over you serial number stencil, building up a puddle of solution.
Remember its the current going through the solution that is doing the etching.
The less you drag the Q-tip the cleaner, even cut you get from the etching process.
You will be able to see when the etching starts. It starts off turning green then brown.
his after five minutes. Etching is just about .005 deep.
You can see how the zeroes middle has started to float off but stayed on long enough to be etched.
After ever thing has been cleaned up. I put numbers from my stencil into the etched numbers.
They will stay there for the rest of the build. After painting and they come off, I will have a shinny numbers easy to see.
Let's do the spider:
You can see how a made a well around the spider so solution well hold in and buildup.
Remember its the solution that does the etching and dragging the Q-tip will give you an uneven cut.
The dark black-brown color show how it's has been cutting.
12 minutes - around .008 deep
I should talk about the solution:
Vinegar, salt and water, I never did measure my mixture. I use mostly vinegar with allot of salt, with a little water.
I don't want to here it, the spell check on my sharpy locked up.
by WE4PONXYZ » Sun May 22, 2022 9:16 pm
Well said Hawkeye and sooo very true.
by Hawkeye » Sun May 22, 2022 2:40 pm
WE4PONXYZ wrote: ↑Sat May 21, 2022 4:12 pmGreat post Hawkeye, soo informative for those looking to get into etching or considering serializing their builds. I have been doing all kinds of detailed hand work all my life so I feel (want) to pass it on to those that can carry on an art that is slowly dying off. CNC machines and computers are the way of the future but for a poor man, doing things by hand is the only option. When I first started, I looked for books on polishing the only thing I could find was from the 50s. So, all that I know has been self-taught. I have been very lucky to have made a 33-year career just doing hand fitting, weld blending and high-end polishing on steel. I had customers from all the sounding states as well as a number of statewide companies coming to me for hand work over the years. When you look back at the custom work done by hand from the time before CNC machines, the old guy had an art that had to be taught to carry on the trade, as time when on more and more custom design is CNC manufactured. With the introduction of 80% build which gave the rebirth of custom one-of-a-kind builds that can last for generations. If I can help keep this art going from father to son and daughter as well as friend to friend that become bothers in custom built arms, that is my goal.
by WE4PONXYZ » Sat May 21, 2022 4:12 pm
Great post Hawkeye, soo informative for those looking to get into etching or considering serializing their builds.
by Hawkeye » Sun May 15, 2022 9:04 pm
I have been busy working on stencils this weekend thanks to rain Saturday and a need to recoup from a day in the sun floating on a kayak. Got all my stencil work for this build finished.
I got so fed-up with not finding the size stencils I needed for my builds so, the end of last year I bought a silhouette so I can design my own stencils and do serial numbers. This is something I should have done years ago. I did a search for art work on the subject I am looking for, you would be surprised at the amount of free art work there is on the net. What I am looking for is a black and white that seems to work best for creating stencils but I have used color art but it takes a little more work. Black and white art you can go straight to the silhouette basic program and make a stencil but with a color art you will take it to a paint shop pro program to turn it into a black and white or a negative for the silhouette program to pick up the contrast in colors. Once you have it in the silhouette program you can change size and just about any shape you need to change. With the spider web I plan on using. I had to make it longer on one end of the web to get it to fit the look I am going for, also with the spider I plan on putting on the barrel, i had to narrow the spider to get it to fit. You can do this in paint shop pro but, it much easier to do after you have you stencil cut lines in the silhouette program. Once you have your stencil just all you have to do is print.
When I make stencils I all ways make more then I need just in case I mess up, I have another one. I use a heat resistant yellow vinyl paper because some times I leave the stencils on during cure time. I do this because if you try and pull your stencils off before you cure your paint sometimes you will pull paint of and you have to start over. Thats a bummer day It is cheaper to buy vinyl in rolls from amazon along with rolls of transfer paper. when I start placing my stencils on this build I will show more tips on using and placing stencils so, for now out till next time.
Had a few hours to work on this build last night.
Where we are at in the process for this build is installing the stencils for the etching process.
Serial number can be tricky to get just right, mostly because they are so small that some of the detail doesn't weed very well. Here you see how the center of the zero's did not come out when I did the weeding. Not a problem, I can find them on the stencil and add them or in this case I just cut some centers out of some 3m yellow tape.
As you can see the centers of the zero's are not perfect. I don't think it is a big deal, when you do your etching those centers will only be there for a short time. They are so small that there is not enough sticky stuff on the back to hold them very long. Your etching solution will sooner or later float them off but they will stay on long enough to get an unetched center, just not as deep as the rest of the zero. Notice how I masked off every thing. Your etching solution is very corrosive, you don't wait this stuff getting on any bare parts or any other parts painted or not. Another reason I am not that concerned with detailed parts of numbers is, when I paint I put the stencil numbers over the etching so that they will be silver and stick out after painting.
Another etching detail on this build is on the barrel. When you look down thou the top slide cut, I want to see a spider in the web. I am very concerned with this, because I have a barrel that I have spent hours of polishing to a mirror finish and is bare metal so, I have to mask off every thing to make sure I don't get any etching solution any where else that would mess up my finish on the barrel. The last thing I want is to repolish around the etched spider.
Before I do any etching I will use a hot air gun to heat the stencils just enough to make the glue backing on the stencils to activate and stick better. Heating stencils also lets you get them into sharp corners and shapes that just a press on will not seal them to keep the solution from leaking where you don't want it to. Another tip with stencils is before you start adding stencils take a clean cotton rag with some alcohol and clean off any oils that my be on you stencil area to insure that you get a good sealed stick. I know I said it before but this is very important you have to have a good stick with stencils to get the solution from bleeding under your stencils.
I'll try to do my etching Sunday, we may have some rain move in so it is indoor projects to work on. I'll take lots of pictures and do a detailed step by step on how I do etching.
by WE4PONXYZ » Sat May 14, 2022 6:31 am
Ancient Order wrote: ↑Fri May 13, 2022 3:53 pmLooks like another Deadpool build in progress! The blade and Ulticlip I did not long ago to accompany a new build that very few have seen yet, it’s hot and I can’t wait to share it with everyone. The barrel in those photos was from when I did the barrel for my DeadPool build.
by WE4PONXYZ » Sat May 14, 2022 6:20 am
Hawkeye wrote: ↑Fri May 13, 2022 1:04 pm XYZ what type of fonts do you use for serial numbers? I use a bold font with sharp conners. I can do whatever you want for RamJetta. I find them easy to burn with least amount of detail. I find when doing small fonts the least amount of detail the better the out come. This will be my first time doing serial #s on a frame plate. But yes I agree, the simpler the font the better the results are. I do have two serial #s to send to you as well in a DM, if you don’t mind making them for me I’d appreciate it very much.
by Ancient Order » Fri May 13, 2022 3:53 pm
Looks like another Deadpool build in progress!
by Hawkeye » Fri May 13, 2022 1:04 pm
WE4PONXYZ wrote: ↑Fri May 13, 2022 9:27 am XYZ what type of fonts do you use for serial numbers? I use a bold font with sharp conners. I can do whatever you want for RamJetta. I find them easy to burn with least amount of detail. I find when doing small fonts the least amount of detail the better the out come.
by WE4PONXYZ » Fri May 13, 2022 9:27 am
I’ve been on vacation for a few weeks but once I get rested up from the long drive I’ll make a new write up for my cheap altoids tin sized “MacGyver” etching setup. Along with some more advanced ones and some links to YouTube tutorials. I’m sure a few of the other guys like @Hawkeye will have some stuff to add to it as well.
by Hawkeye » Thu May 12, 2022 5:32 pm
Ancient Order wrote: ↑Thu May 12, 2022 2:39 pmHawkeye wrote: ↑Wed May 11, 2022 10:47 pmAncient Order wrote: ↑Wed May 11, 2022 8:47 pmI have an idea for some etching on a slide for an upcoming build, so details would be appreciated What kind of stuff you need? Well, I know zip about etching but I have at least one slide that's BEGGING for some. If you can point me to a good resource for learning how to do it, that would be great! I will do detailed step be step on how I do etching in a week or so. It's really easier than it sounds. Anything I can do to help.
by RAMjetta » Thu May 12, 2022 4:00 pm
Ancient Order wrote: ↑Thu May 12, 2022 2:39 pmHawkeye wrote: ↑Wed May 11, 2022 10:47 pmAncient Order wrote: ↑Wed May 11, 2022 8:47 pmI have an idea for some etching on a slide for an upcoming build, so details would be appreciated What kind of stuff you need? Check the resource section sir. I believe Hawkeye or We4ponXYZ have posted instructions in there. Well, I know zip about etching but I have at least one slide that's BEGGING for some. If you can point me to a good resource for learning how to do it, that would be great!
by Ancient Order » Thu May 12, 2022 2:39 pm Hawkeye wrote: ↑Wed May 11, 2022 10:47 pmAncient Order wrote: ↑Wed May 11, 2022 8:47 pmI have an idea for some etching on a slide for an upcoming build, so details would be appreciated What kind of stuff you need? Well, I know zip about etching but I have at least one slide that's BEGGING for some. If you can point me to a good resource for learning how to do it, that would be great!
Top
by Hawkeye » Wed May 11, 2022 10:47 pm
Ancient Order wrote: ↑Wed May 11, 2022 8:47 pmI have an idea for some etching on a slide for an upcoming build, so details would be appreciated What kind of stuff you need?
by Ancient Order » Wed May 11, 2022 8:47 pm
I have an idea for some etching on a slide for an upcoming build, so details would be appreciated
by Ancient Order » Wed May 11, 2022 8:46 pm
Looking good! Can't wait to see the next installment
by Hawkeye » Wed May 11, 2022 3:41 pm
I've been sanding away
Next, making a stencil for serial numbers, then etching them on the frame.
All so make the rest of the stencils, web and spider for another sandblasting before more polishing and paint.
Thing will probably slow down now. It is summer and there is just to much other stuff to do now, among them garden, flower beds, honey dos, kayaking and my favorite night fishing. I know it sucks but someone has to do it. Live Free till next time
by Ancient Order » Sun May 01, 2022 9:19 pm
Next episode!!
by Hawkeye » Sun May 01, 2022 8:36 pm
I have been hard at it this weekend catching up on this turn of events with this build. I tried but I am not as fast uncle Joe Bidin, just drilling and taking off tabs when lapping out pin holes took me every bit of four hours. No matter how hard I practice I'm just not as fast as Joe. So, let's get started on the frame:
This stuff drives me nuts, in the cercle is a mark made by a short injector pin witch leaves a mark. This will all ways show even after you paint unless you remove it along with the parting line (lines from the two halves of the mold being worn and not meeting flush). It is not that of a big deal for me because I sand or blast before I paint but newer builders don't and they have to put up with this blemish until they sand and paint. ME I rather buy my frames smooth without any texture so that would save me a lot of sanding time.
Those of you that have seen so of my build, know I do lots of mods to my frames so, here we go:
This is a small pocket pistol and does not need a flashlight, so the first step is to remove the rail. I have three different ways and looks I do this one is the easiest.
I hate square triggers so it has to go remember this is a pocket pistol they need to be as small as you can get them SAFTLY. First I work on getting the trigger shape ruffed out then I like to narrow the trigger.
At .470 for me this is just to wide but most holsters need that wide trigger to latch on to.
The trigger that are on P-80s just have no style to them at all so I will narrow they giving them some shape.
Now that I have ruffed out and shaped the trigger Its time to fill in the part of the rail with JB Weld. This is very easy just add some tape to hold the JB Weld in place until it sets up.
After the JB Weld set up all I have to do is blend to shape.
Now I start rounding off the sharp edges for a more high end look.
I think a molded part that has a lot of sharp edges looks cheap. If anyone in interested in why just ask me and I'll do a rant for you but for now I will spare you guys.
Now I have a lot of sanding to do this week If I can find the time with garden, fishing and honey-dos time is hard to come by.
by Ancient Order » Fri Apr 29, 2022 8:56 pm
Yeah, with the slide you got going on, you need a lower you're happy with.
by Hawkeye » Fri Apr 29, 2022 7:14 pm
So, I got a chance to do some work last night, JB Weld has set up and ready for blending. Those black spots are shadows, the blend looks ok, but I can do better.
This build is taking on a life of its own now and I am NOT happy with using this ss80 for a top quality build.
This is one of four ss80s I build year back when I first started building. Only two are left and shootable builds.
I don't know if anyone has had the disappointment I have with ss80 but, (IMHP) they suck and don't hold up to long time shooting and donot hold up when taking them apart over and over. Two of my ss80 have stress cracks next to the slide stop, one cracked and I fixed by using JB Weld to mold a staple in for more strength.
So, after putting so much time into the slide I am going to do a recall on these ss80 and build a new PF9ss frame for this build. After all Its FRIST TIME QUALITY right? I will return these two ss80 to the, I fuck up ben of stuff I have messed up in years of learning how not to do something.
Anyway this ss80 has been so abused in the past I can't get the high polish I need to make the Black Chrome paint to pop.
With a build this intense I think it needs a better stippling lob too.
by Hawkeye » Fri Apr 29, 2022 10:46 am Ancient Order wrote: ↑Thu Apr 28, 2022 9:17 pm Might also give the impression of spider webs [/quote] This gives me an idea!! what if I make the web a sand blast and leave it with just a clear coat. That would give me the silver web. I would have to mask off the high polish finish but I think I can do it. Then I could sand blast the spider on the barrel to match. What do you think?
Top
by Ancient Order » Thu Apr 28, 2022 9:17 pm
Hawkeye wrote: ↑Thu Apr 28, 2022 10:27 amAncient Order wrote: ↑Wed Apr 27, 2022 11:13 pmLeave the serrations rough but mirror polish the ridges That would make them pop more. I'll give it a try but I have to be carful not do mess up the blasted area. I don't want to sand blast again. Might also give the impression of spider webs
by Hawkeye » Thu Apr 28, 2022 10:27 am
Ancient Order wrote: ↑Wed Apr 27, 2022 11:13 pmLeave the serrations rough but mirror polish the ridges That would make them pop more. I'll give it a try but I have to be carful not do mess up the blasted area. I don't want to sand blast again.
by Ancient Order » Wed Apr 27, 2022 11:13 pm
Leave the serrations rough but mirror polish the ridges
by Hawkeye » Wed Apr 27, 2022 10:38 pm
RAMjetta wrote: ↑Wed Apr 27, 2022 8:37 pmI'd leave the serrations rough Thats what my wife said, she is my go-to for bouncing ideas off of. I finished polishing the slid today and by leaving the serrations rough it just adds another dimension. Now getting the frame up to a higher polish to match the slide.
by RAMjetta » Wed Apr 27, 2022 8:37 pm
I'd leave the serrations rough
JettaMan OUT!
by Hawkeye » Sun Apr 24, 2022 8:30 pm
I got a chance to work on this build a few hours so here is where we are now.
After doing some heavy sanding to remove old paint and removing some bad scratches we're at the first stage of sanding. The sanding on this rebuild is not what you will run into on a new build so don't think you have to go this extreme for a fist time quality build and paint. This ss80 has been blasted by some very course sand in the past that I did to see if I could come up with a texture technique to keep from doing as much sanding. It really didn't come out the way I wanted so this became my test build for every Idea I had that needed to be tested before I worked on my theme builds, that's why this one need so much sanding and blending.
Here is what I used for the heavy sanding and the blending of the scratches.
Remember this is not (do this step then do this step) this is a process of knowing how to remove scratches.
1) Cera points: info from
https://www.gesswein.com/abrasives/rubb ... era-point- starter-set/
Wondering which grit of CERA will work for your application? Try our money-saving set of the most popular 5 x
15 shape. One of each grit (red 80, blue 120, green 220, purple 320 and orange 500). Coarser grits (red, blue)
cut quickly; medium (green, purple) remove light scratches; fine (orange) removes fine scratches and leaves a
smooth finish that is ready for polishing.
This revolutionary product contains ceramic particles mixed in a rubber carrier. Its special properties allow the
ceramic abrasive to always be exposed to the polishing surface, ensuring high efficiency and no clogging. For
soft (gold, silver) and hard metals, including steel, stainless steel, and platinum.
I use these a lot over the years on steel but they work great on plastic and polymer, just be carful not to let
them get hot melting the plastic or polymer.
2) These are scotch pads on wheels and come in different grits too and all so will melt plastic and polymer if let
setting in one spot building up heat.
3) You have to be very carful with these. They come in all grits from 80 to 600. On plastic and polymer I only use
400 and 600 grit. If you look at some of my builds you can see that I remove a lot of material rounding edges,
taking out the square triggers. this is what I use for that but just as a roughout step.
4) This is the greatest tool ever made for the kind of sanding I do on my build. I was turned on to this by Racer88
(I think) back in the MGB days. It is a Micro Sander from "Micro Mark" I bought mine from Amazon with free
shipping. You can get 320-400-600 grit that just sticks on. This has really changed the way I sand now and is a
must have for me.
I'm not going to give you a step by step because this is not what happens. You start off switching between all the different techniques. The only step I will stick with to go over the whole build is wet sanding.
So the next step is to come up with a way to clean up the stippling and fix holes, then It will be time for some wet sanding.
Got a few hours in yesterday so here we go:
As you can see I added some tape to keep the JB Weld from getting onto the frame
making it hard to clean up later.
You will still need to use some sand paper or a small fine file to make sure there is not any drag on inner parts.
Just a little bit of JB Weld is all I need. Before I did the JB weld fix I when over the grip with three different size ball diamond burs. Yes every little dimple to clean them up. Took me all most two hours.
I need a little in put here, I'm not sure about where I'm going on this build
(Happens every build, they all ways take sidetracks.)
While I was waiting on the JB Weld set I started polishing my slide to a high polish (mirror finish) and I left the serrations with a blast texture. I plan on painting the high polish in a black chrome. WHAT!! I WANT SOME INPUT ON IS, do I leave the blast finish (serrations) or polish it to a high polish for paint. When I do a web on this Black Widow build I was thinking a silver color. Not sure on the grip color yet so if you guys have any ideas I would be glad for some input. I'm kind of leaning to a flat black grip with a black chrome pistol and a silver web. What do you guys think???
by Ancient Order » Thu Apr 21, 2022 9:18 pm
Ready for Episode 2!
by WE4PONXYZ » Thu Apr 21, 2022 3:10 pm
Looking forward to it man, sounds like you got a plan already that is a cool concept.