by WE4PONXYZ » Sat May 28, 2022 12:36 pm
Alright sooo I know quite a few people have been curious about my wallet tin sized etching kit sooo I’ll do a break down of what I have in there currently. P.s this kit is small enough to fit in a large altoids tin as well, I like this slightly larger one as I can keep vinyl, stencils and more pads in it. Only thing my kit is currently missing is some small gator clips. Eventually I plan to hook up a switch and battery compartment and upgrade to some thicker wires. As I continue working on this project throughout the day, etching some personalized serial number plates I will post photos and commentary along with answering questions. Right now I’m just prepping before starting to weed/pluck/pick the serial number stencils and get all the frames I’m doing prepared. Big shoutout to @Hawkeye for the serial plate clamp idea. Sooo that was the first thing I made today, I used one half of an steel L bracket, btw the hole closest to the cut is a perfect match up to the plate connection inside of the dust cover/channel. I then used two nuts and a bolt that I ground down into a flat cone tip to go into the little recess where the connection to the plate is.
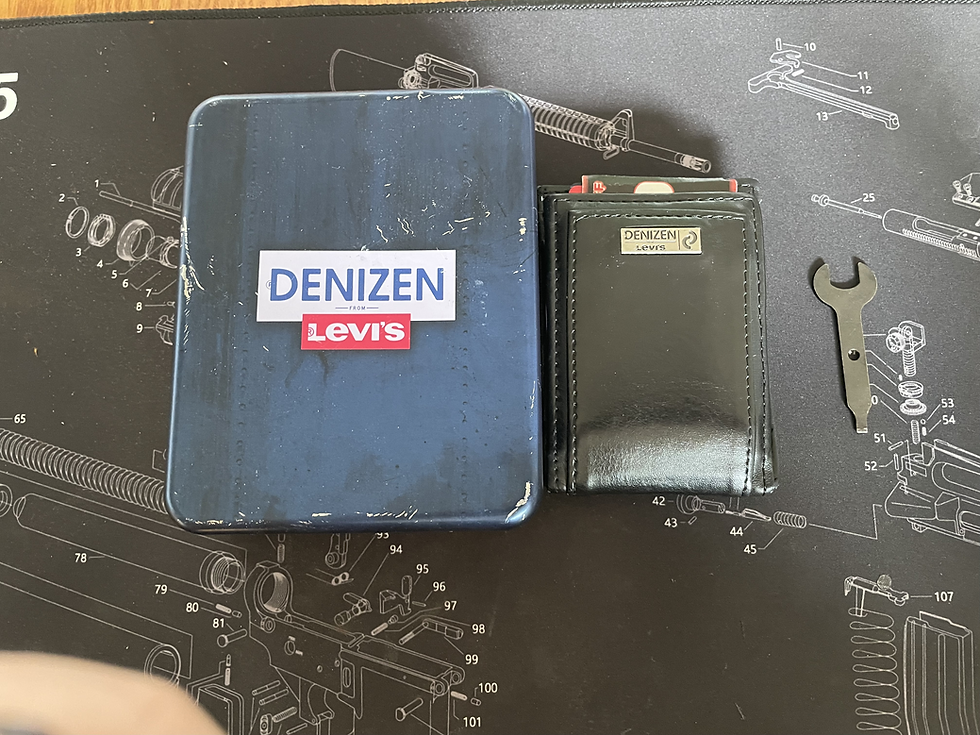
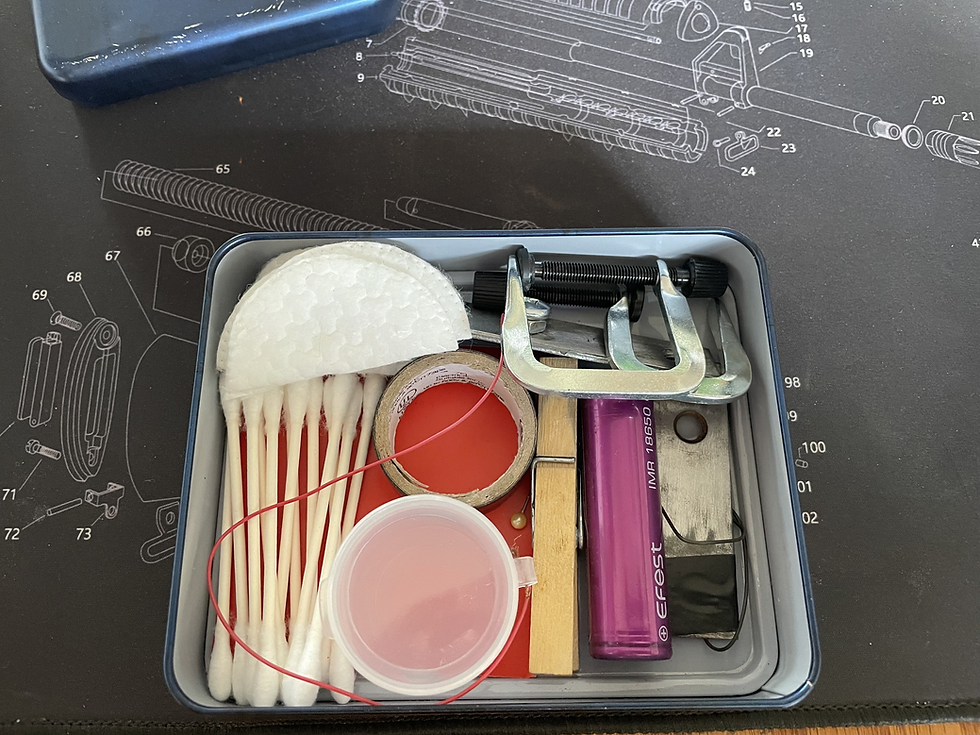
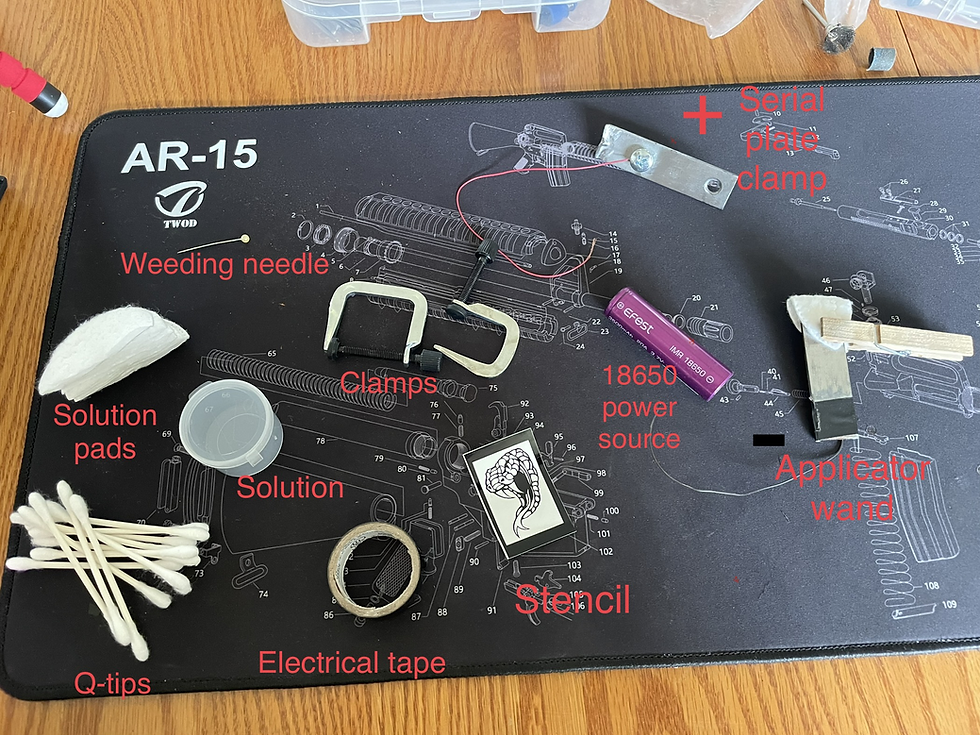
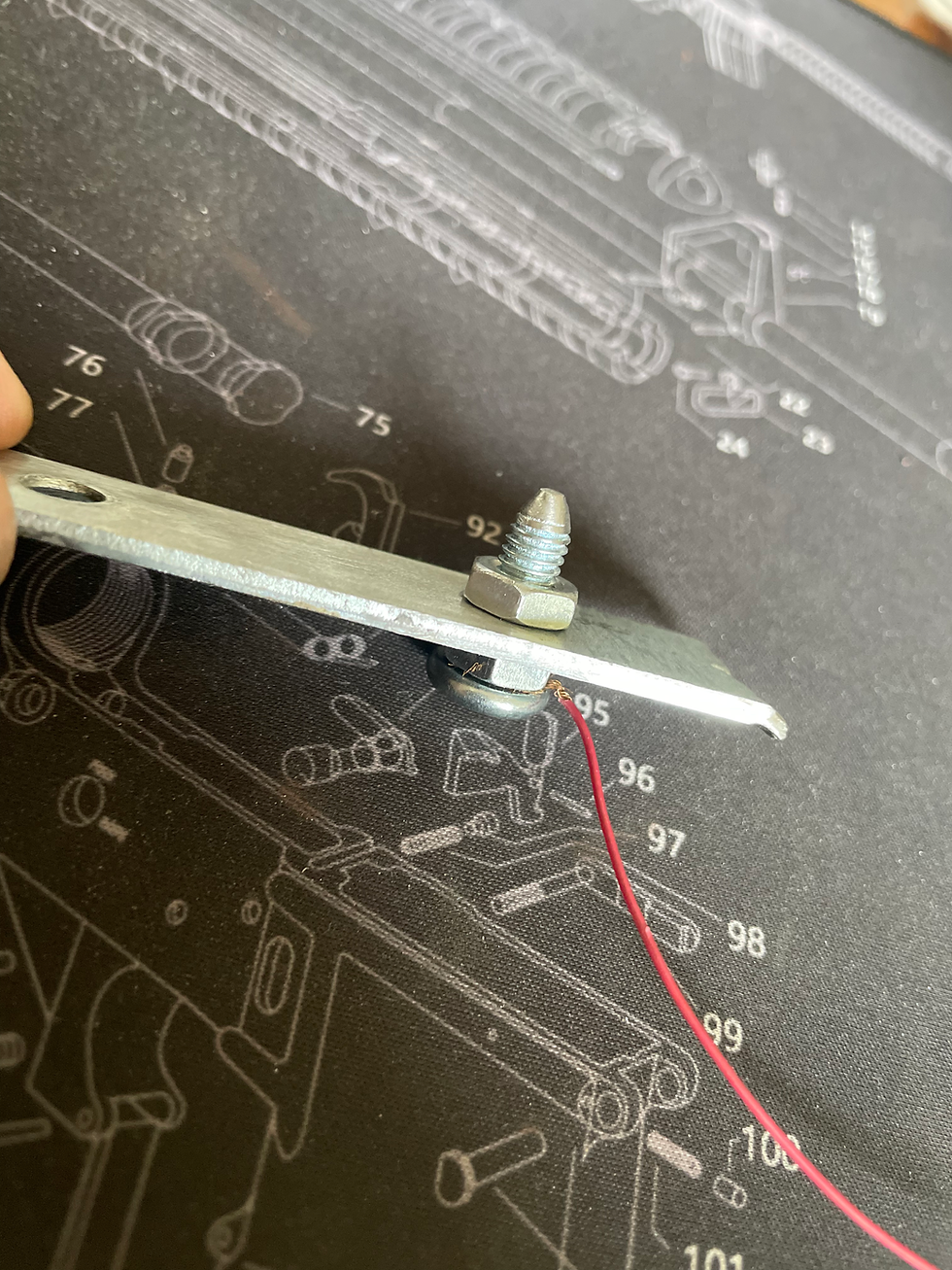


by WE4PONXYZ » Sat May 28, 2022 9:49 pm
This was a stainless bottle I did for my wife last year with a cute little penguin on it. I used the same kit to do it. As @Hawkeye said stainless steel can be finicky, especially these type of stainless coffee mugs and such. They don’t etch very deep but you are left with a really cool contrast in the appearance of the metal due to the chemical reaction.
by WE4PONXYZ » Sat May 28, 2022 9:19 pm
Ancient Order wrote: ↑Sat May 28, 2022 1:27 pmThis is totally new to me, so I appreciate all the info. I'm trying to understand the "science" behind this process and the different parts/pieces used when etching. Layman’s terms: (for me not you) Basically the main science behind it is you are completing a circuit to whatever object you are etching. You need a power source connected via wires positive (to object) and negative (to applicator). A metal applicator of some sort to hold your solution which is basically Salt+++ Vinegar and water (I use cut up makeup rounds and a Piece of metal). When the circuit is completed a chemical reaction occurs and eats away at the metal that’s not covered by the stencil. This can also be done on projects by creating a well around your stencil with hot glue and filling with the solution or by suspending your negative wire/applicator in a vessel filled with the solution and your part inside taped off to etch. Most important thing to remember is that anything metal that is connected to the circuit will be effected by the solution if its exposed.
by WE4PONXYZ » Sat May 28, 2022 3:40 pm
Alright soo “DeadPool” is all done, using the clear nail polish worked like a charm and it turned out great. As long as I didn’t over saturate my etching area my solution stayed where I wanted it. Using the large wand/applicator allows me to cover the whole area without needing to rub which can cause the vinyl to come up.
This is a stamping method you want to keep your applicator moist and saturated but not dripping. I use the side of my vessel that my salt solution is in to scrape off excess. You wanna apply light downward pressure, if your stamp/wand isn’t wide enough then keep moving it around in stamping motions. I set about a 10 min. timer which seams like the perfect time for a nice deep etch on the plate. This method is perfect for small detail etching like letters and numbers as the vinyl is less likely to peel back or solution get under it.
by WE4PONXYZ » Sat May 28, 2022 4:41 pm
The second one I did turned out even better, as I now know how fast the material etches. I’ll be covering up parts of the serial numbers, not that I don’t trust y’all. I just don’t trust the Looky Lou’s!!!
by WE4PONXYZ » Sat May 28, 2022 9:04 pm
After I pluck and cut my stencils for the serial plate, I then sandwich it between the transfer paper. After smoothing out my image with a flat edge I then peal back the backing from the transfer paper and stencil backing. I replace the transfer paper backing and cut my stencil down to a little pull tab so I can apply it and remove the transfer paper easily
by WE4PONXYZ » Sat May 28, 2022 9:12 pm
I did 6 frames today on a single charge of the 18650 battery. All 6 turned out fantastic, deeply and sharply etched. I’ve used various different methods including expensive setups. I used to use a large golf cart charger, but ya gotta plug it in and it takes up space. I put this tiny setup together with literal garbage and scraps laying around the house in like 20 min. The little clamp device I made today to contact the serial plate did take me an additional 20 10 of that was hunting for just the right bolt and nuts!!! Learn, Innovate, share!!!
by Hawkeye » Sat May 28, 2022 3:15 pm One thing to remember is that the metal that the serial number is being etched on is a tin-zinc mix and will etch faster than say a solid stainless-steel slide and will not cut as sharp and clean. The reason for this is the impurities in the tin-zinc mix. so don't try and do a deep etching to keep it clean looking. I would not try to etch any higher than 10A. I used a 50A once and found it to be hard to control for an even cut but I was using a battery charger that can hold a higher steady currant. Another thing about stainless-steel is, it too has its quarks about etching, it has chrome mixed with the steel. That's what gives it the rust resistance, but it can cause pits when etched too deep and too fast. I guess a good rule of thumb is to go slow, that way you can control the etching process. This is just what I have found in doing my etching. One of my jobs was using an industrial chrome plating tank of small job fixes in the shop I worked. Plating is the same thing as etching except in reverse with a different solution mix.
Top
Oh yeah no worries, I’ve done like 6 different projects with this battery ranging from very small to a large stainless steel bottle. Once I’m done with my project I disconnect both the +\- from the battery and put tape over the connections as well. Safety 1st
It’s a 10A continuous discharge which is absolutely perfect for electro etching.
by WE4PONXYZ » Sat May 28, 2022 1:58 pm
I’m starting with one of my builds for the serial number etching. Since I use my rail and it is a PITA to tape around the serial number with it there. I’m applying a clear coat polish around the edges of my stencil, anywhere that metal is exposed that I don’t want etched. The clear coat will act as a protective layer between my salt/vinegar/water solution and the metal. This will also speed up the process significantly as I’ve got quite a few frames to do.
by sailman » Sat May 28, 2022 1:32 pm
I know you've probably already thought about this but have you checked the Amps to see what your draw is going to be on the battery. Don't hold me to it but I believe that the battery has somewhere between 20 and 35 Amp maximum draw I'm not sure what the pulse on it is, It should be listed on the side of the battery. Like everybody has always said safety is our 1st priority, just don't want that thing to go off in your hand. I just looked at your picture and you've got a 20 amp battery so just be careful.
by Ancient Order » Sat May 28, 2022 1:27 pm
This is totally new to me, so I appreciate all the info. I'm trying to understand the "science" behind this process and the different parts/pieces used when etching.