by sailman » Sat Jul 23, 2022 10:31 am
Alright trying to get this great ghost slide put together. I'm having a little issue with the extractor plunger and the screw used to hold the RMR cover plate. When everyone has this issue of the screw being too long how do you secure in the screw so you can file and send it to fit? Let me tell you my pointer finger and thumb are killing me from trying to hold it.
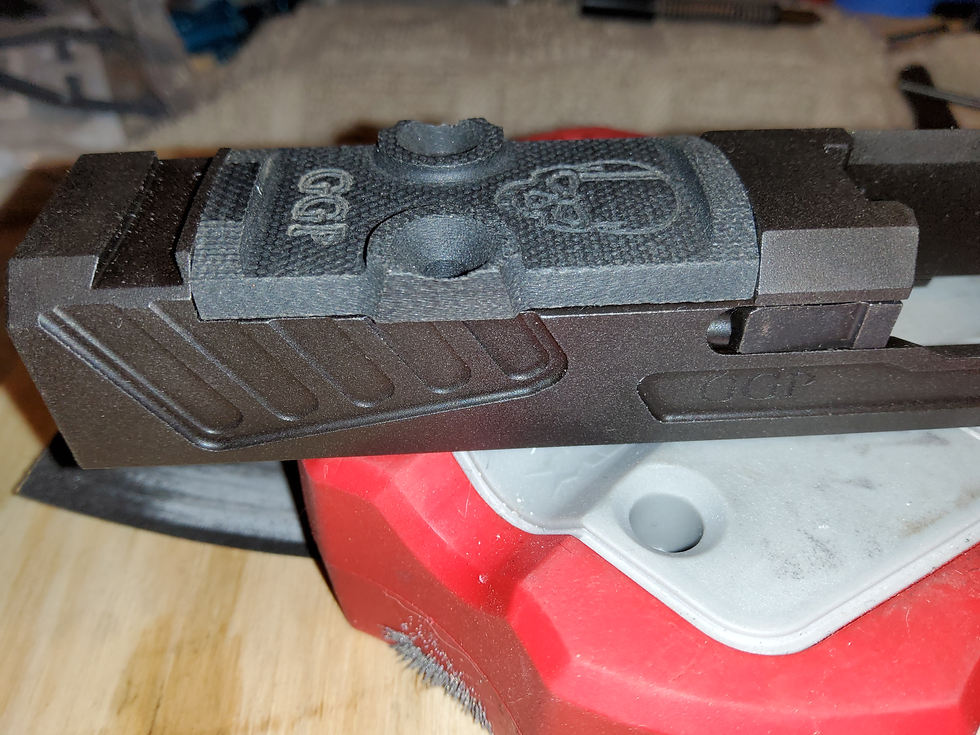

by sailman » Sat Jul 23, 2022 1:57 pm
Ancient Order wrote: ↑Sat Jul 23, 2022 1:26 pmNo offense Sailman, but that RMR cover is butt ugly and doesn't match. Might be just the picture, but I'd replace it with a metal one that fits better. As for the screws, if I have to shorten one I use a nut of the correct size screwed down to where you want to cut or grind to. it will also help to hold the screw in a vise when working it. Oh yeah I'm right there with you on that. That will be one of the 1st things that gets changed out after I get it up and running.
by Ancient Order » Sat Jul 23, 2022 1:26 pm
No offense Sailman, but that RMR cover is butt ugly and doesn't match. Might be just the picture, but I'd replace it with a metal one that fits better. As for the screws, if I have to shorten one I use a nut of the correct size screwed down to where you want to cut or grind to. it will also help to hold the screw in a vise when working it.
by Steelart99 » Sat Jul 23, 2022 11:54 am
I know it takes a bit more "tooling", but when I shorten screws, I get a brass or steel plate with a thickness about equal to about the length you want the screw to be and about 1"x3" size. Tap the appropriate size hole through the plate somewhat towards one end of the plate. Screw the screw into the plate and then grind the "extra" length off the back side using a die grinder or sander or file or whatever, until the screw is flush with the bottom of the plate. You can clamp the plate into a vise to make it easier to file, or just grip the plate and rub the screw on sanding paper or use any type of sanding machine. Obviously can be used again. BTW, if you need a longer screw than what the plate is specifically designed for, you can use the same plate, just stick a washer (or many washers) under the head before screwing the screw in. Then follow the same procedure. FWIW, I'm a knifemaker and use this method on all the 0-80 screws that I use in assembling my folding knives.
by RAMjetta » Sat Jul 23, 2022 11:29 am
Hawkeye wrote: ↑Sat Jul 23, 2022 11:03 amI have this problem a lot. For a small screw like this one I use my dermal with a diamond bur or a medium grinding wheel to shorten it, then bevel the tip so the treads will start back in the hole. If you need to take a wire brush to knock off the burs. I have used this method for years, seem like all the screws and bolts I have saved over the years they are all ways to long. OH! I use a small one-inch vise to hold the head of the screw or a channel lock plyer because of the heat build up (you can't hold it). #BurntFingersSuck ask me how I know. Lmao
JettaMan OUT!
by sailman » Sat Jul 23, 2022 11:18 am
Thanks guys I'll try those suggestions
by RAMjetta » Sat Jul 23, 2022 11:07 am
Lol...two words (or three) Pier's/vice and Dremel or Rotary Tool. Of course, it depends on how much you want to cut or sand.
JettaMan OUT!
by Hawkeye » Sat Jul 23, 2022 11:03 am
I have this problem a lot. For a small screw like this one I use my dermal with a diamond bur or a medium grinding wheel to shorten it, then bevel the tip so the treads will start back in the hole. If you need to take a wire brush to knock off the burs. I have used this method for years, seem like all the screws and bolts I have saved over the years they are all ways to long. OH! I use a small one-inch vise to hold the head of the screw or a channel lock plyer because of the heat build up (you can't hold it).