I have molded in magwells for a few years now and have a sloid way to make them look like is a solid part of the frame.
First make sure you are using the right JB Weld.

When you sand off the factory stippling, the magwell don't fit as tight as they would if the factory stippling was still there. You can fix this by use a stippling boarder ( Glendhill Custom video on boarders on you tube) or use JB Weld to fill in the gaps.


So what do we do with the screw? I have use two methods, modify the screw or use a reset screw, but this only works if your going to use a stick-on rubber grip, this lets you cover a reset screw but doesn't work for custom stippling.
Here is a good example of how this doesn't work for custom stippling.

Here is what you can do to mold in a magwell and still do custom stippling. You can use a reset screw or grind off thr outer part of the head so you can recess the head.
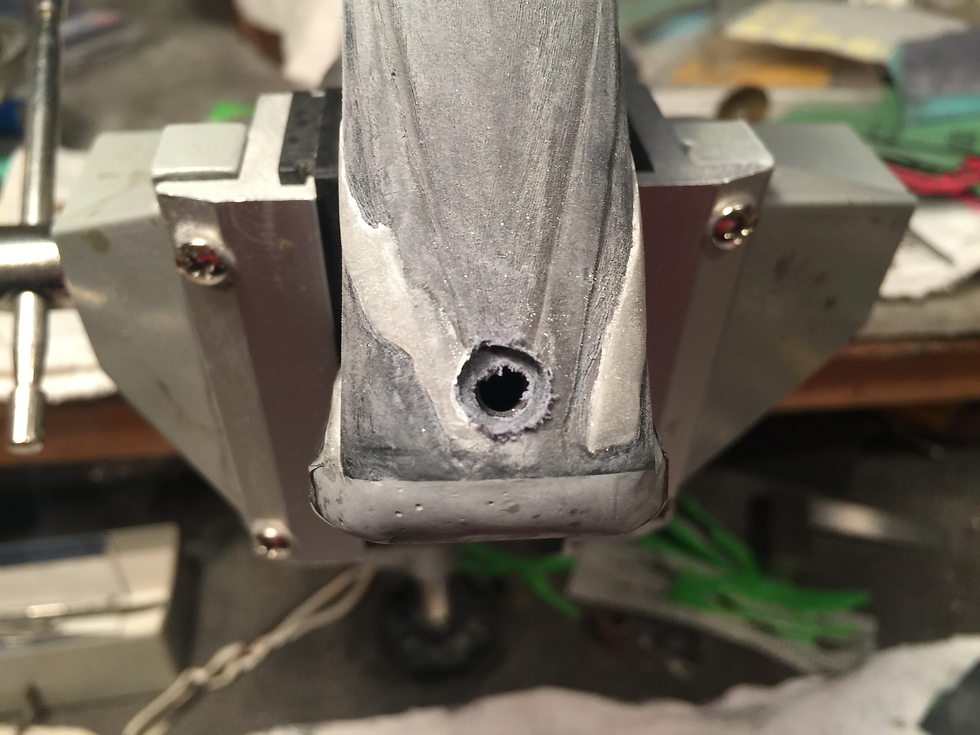
So what now? This is why you need to save the tab you cut off your frame. I took a tab from this build and melted it in to the hole on top of the recessed screw, and then sand. This lets you do custom stippling that matches.
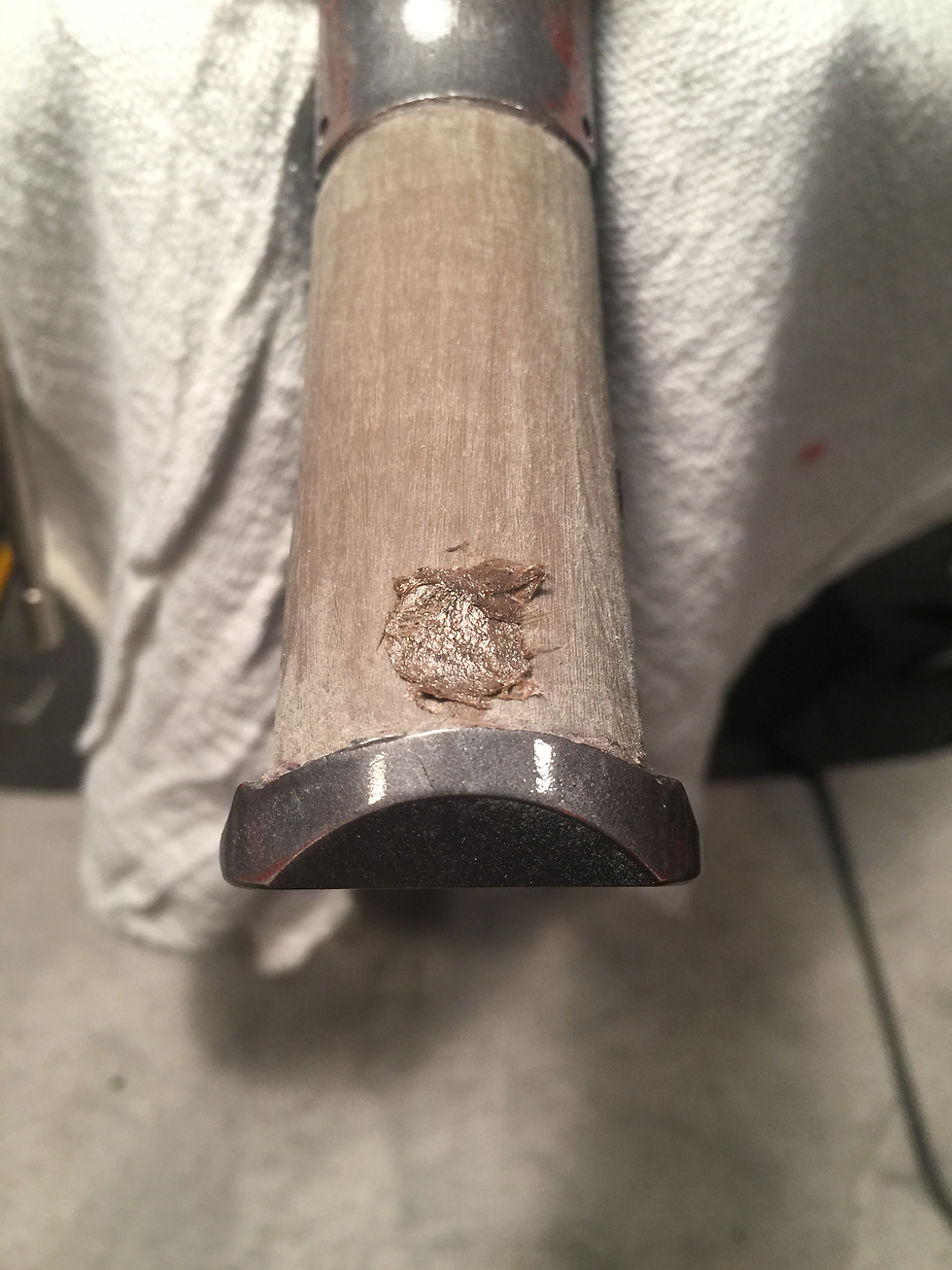
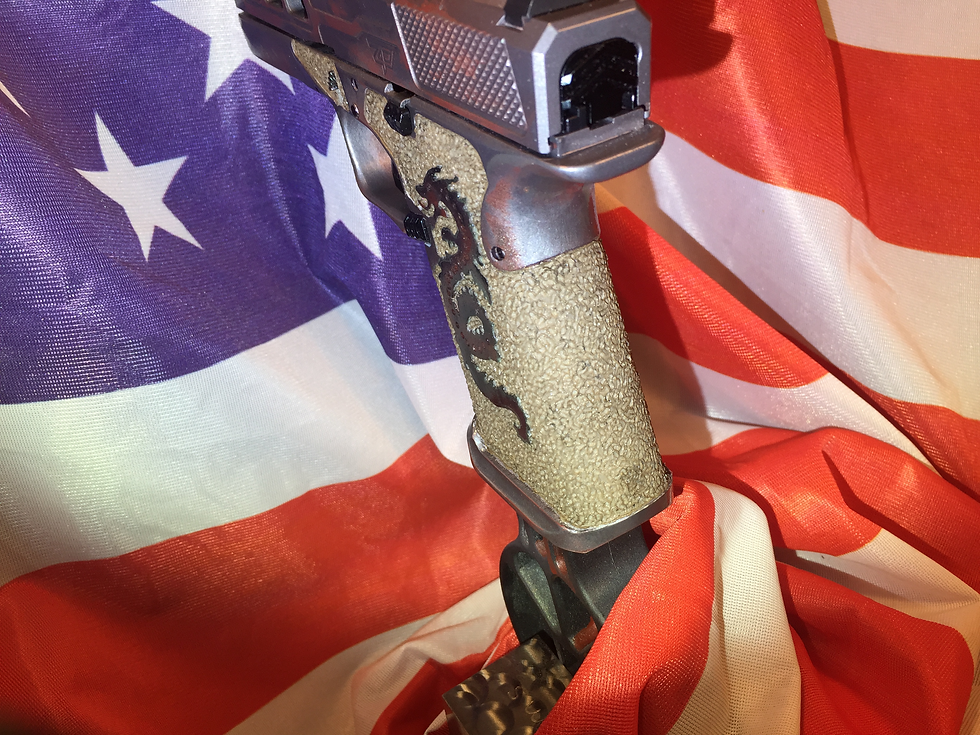
Another idea I had was to design your grip to cover the screw hole.
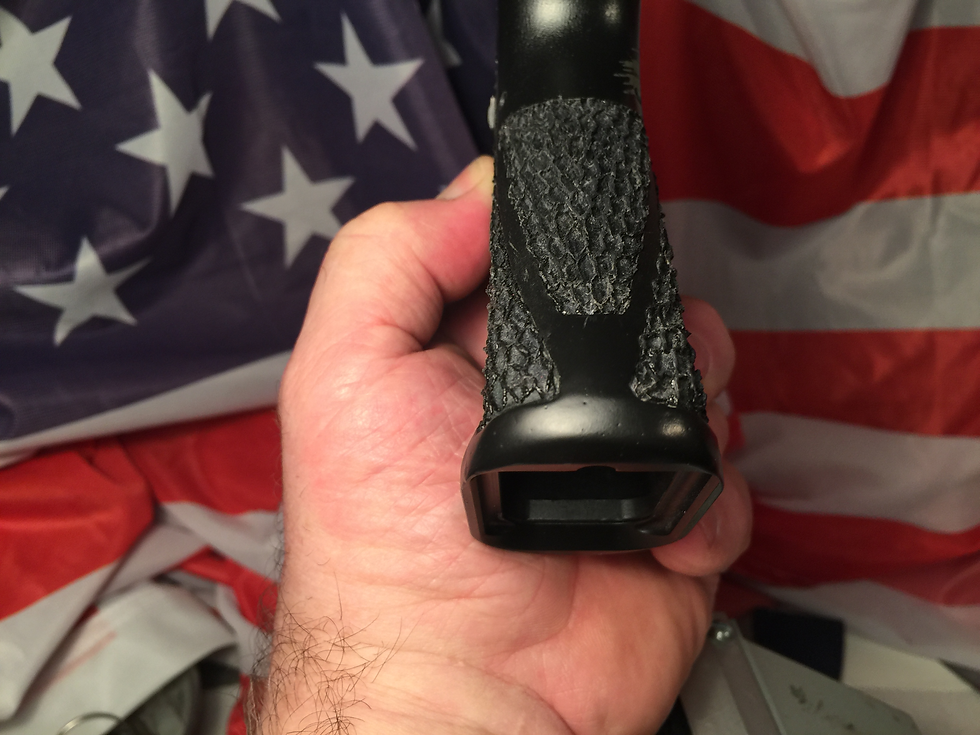
It all comes down to planning before you start. I'm sure there is other ways to do this, and I'm sure in future builds I'll come up with other ways, these are just some that I have done to my builds so I know that they work.
Hope this helps take your builds to next level.
by Hawkeye » Tue Oct 18, 2022 4:06 pm
This is a Lone Wolf magwell.
I molded or should I say glued in this magwell with Loctite 380. This is the same stuff that I used to glue in the rails on the LW.
Here I already added some JB Weld but using the dab and pat method it has some pen hole that need a fix.
The shape of the LW magwell has some real problems, it is just not comfortable to the griping of the pistol. In my post "Freedom Wolf part 1" I showed how I tried to address some of these problems but here I am dealing with the shaping of the back part of the wagwell that has a good mounting idea but as far looks it is not high-end looking stuff.
After opening up these pen holes with a ball diamond burr, I mixed up some JB Weld and let it set for about a half hour or so. This lets it set up to keep it from being so runny. Then I added a large amount but not more than I could control with a little stick for moving it around.
Here is the trick in using this mothod, I have the pistol in a 360 vise so I can turn it over side to side and even upside down. This may take an hour or more depending on how much you let your JB Weld setup before adding it to you magwell. Keep turning your pistol letting the JB weld run one way then the other until you have JB Weld coving everything you intend to coat. After a while it slows to the point it stops running, just let it sit till cured and sand to shape. I'll have a picture when I get it sanded to shape.